Forged wheels are renowned for their strength, durability, and lightweight properties, making them a premium choice in the automotive industry. However, achieving the perfect finish on forged wheels requires precision, efficiency, and advanced surface preparation techniques. Abrasive media grinding machines are designed to meet these demands, offering exceptional results for forged wheels. Below are the key benefits of using these machines specifically for forged wheel processing:
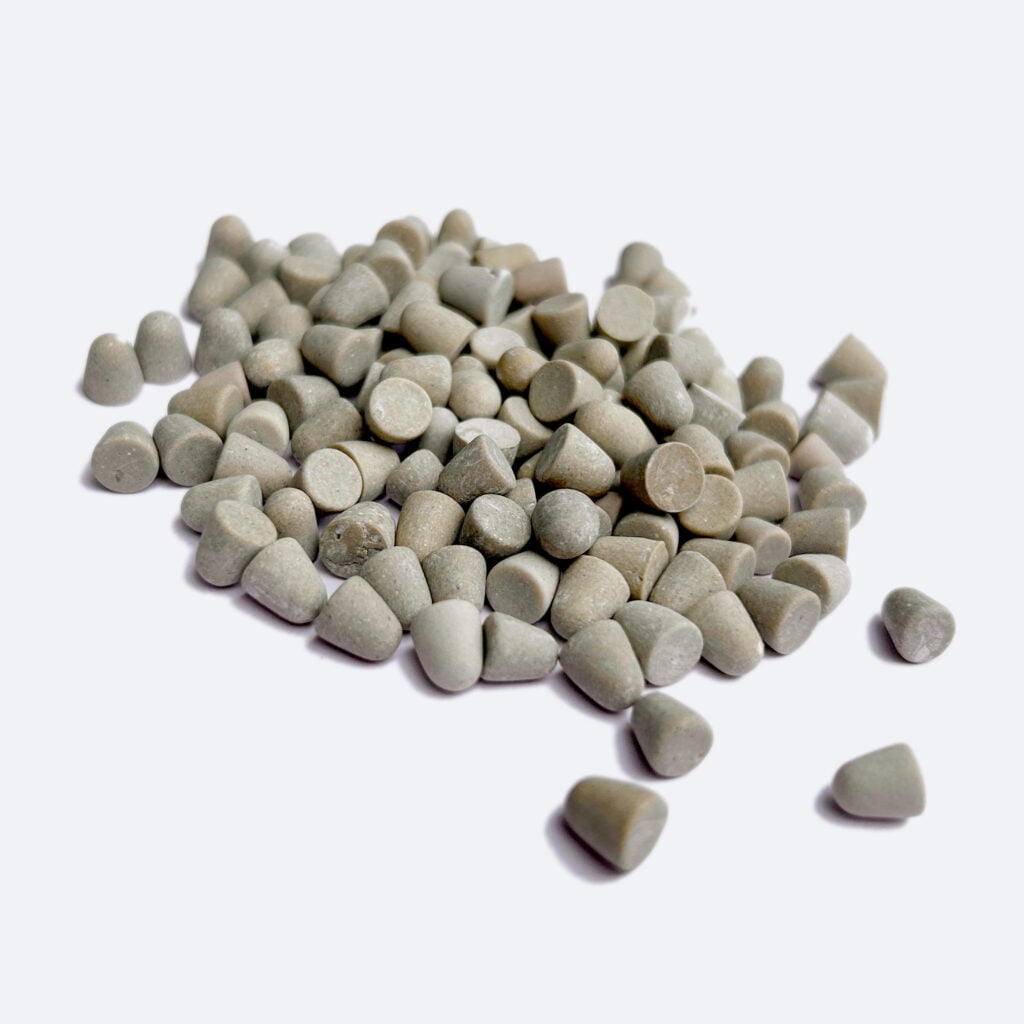
1. Superior Efficiency in Forged Wheel Finishing
Forged wheels often involve intricate designs and require precise finishing to enhance their aesthetic and functional appeal. Abrasive media grinding machines streamline this process, providing:
- High throughput: The ability to process multiple wheels simultaneously, saving time and increasing productivity.
- Reduced manual labor: Automation reduces reliance on hand polishing, cutting costs and minimizing human error.
- Faster turnaround times: Optimized machine settings allow for quicker finishing without compromising quality.
2. Compatibility with Forged Wheel Designs
Forged wheels come in a variety of sizes and designs, ranging from simple to highly intricate. Abrasive media grinding machines are highly adaptable, offering:
- Versatility: Capability to handle wheel sizes up to 32 inches and various spoke designs.
- Precision for complex geometries: Media and machine settings can be fine-tuned to work on detailed patterns without damaging the wheel.
- Uniform coverage: Ensures that every part of the wheel, including inner spokes and corners, is evenly finished.
3. Achieving Smooth and Uniform Surfaces
Forged wheels demand a flawless surface finish to highlight their premium quality and ensure optimal performance. Abrasive media grinding machines deliver:
- Burr-free edges: Precision grinding eliminates sharp edges and imperfections caused during forging.
- Consistent results: Advanced technology ensures every wheel in a batch meets the same high standards.
- Improved aerodynamics: A smooth surface enhances the wheel’s performance by reducing air resistance.
Raw rims after CNC can have intense machining marks, and it will take a long time to sand to powder-coating rims, let alone polish rims. But with our rotary polishing machine, you will only have to load the rims to the machine, and then 10-40 minutes later, they will be ready for powder coating.
Let’s check out rim performances when you use our coarse media 6*6mm to polish.
Without any polishing tools, only with media and compounds, you will get to know how to polish aluminum rims!
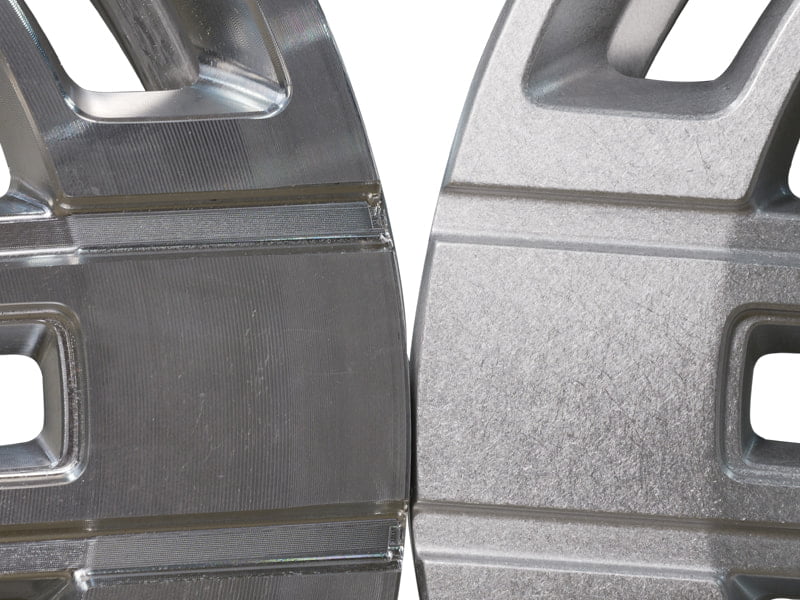
Below is the rim performance using just rotary machine polishing:
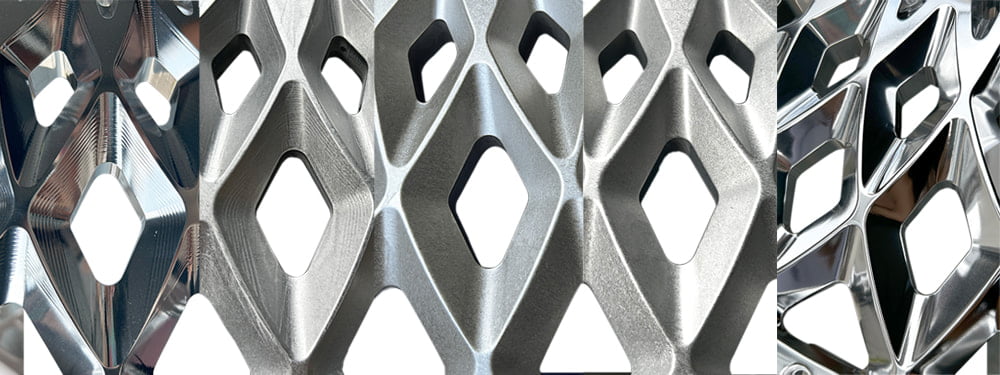