The complexity of rim design requires various polishing tools if polishing by hand. For different batches of rims, it can take hours to finish one rim.
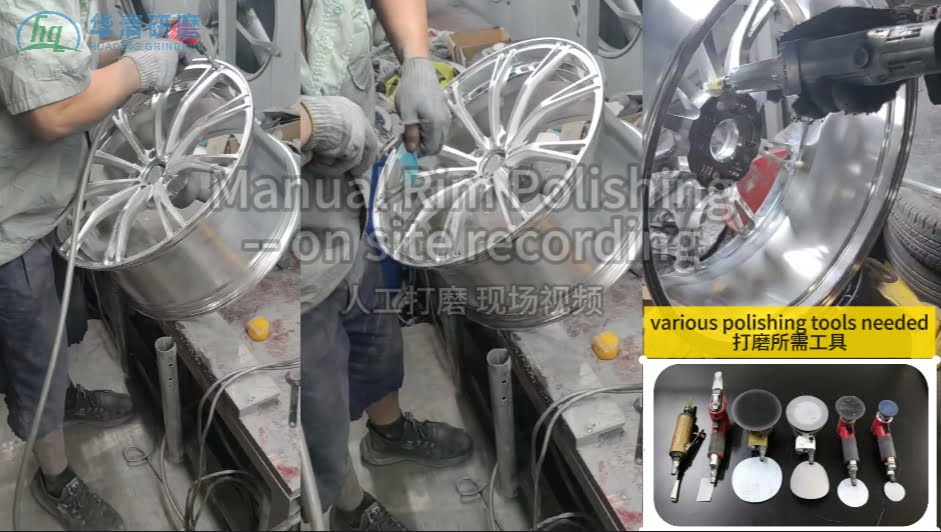
Rotary ceramic rim polish machines offer several key benefits, making them popular in automotive and industrial settings domestically. Here are some of the primary advantages:
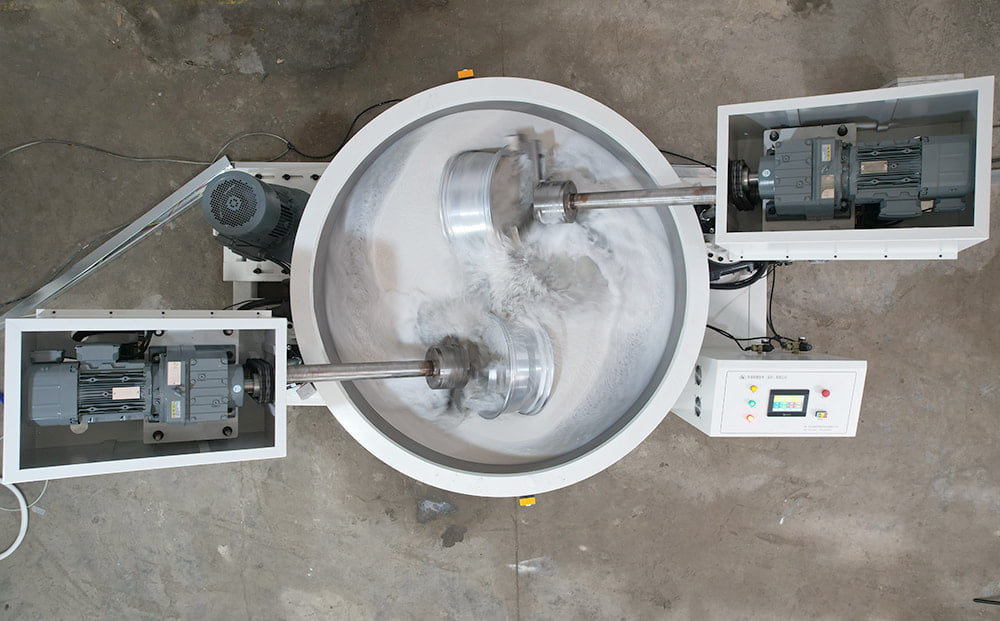
Compatibility and Versatility :
- The ability to handle wheels of different sizes (up to 32″) for both trucks and cars, allows for versatile use across various types of rims.
- The capability to process both forged and cast aluminum wheels with minimal variation in consumables (media and compound) simplifies operations.
Cost and Time Efficiency :
- Significant reduction (more than 60%) in manpower required while maintaining production capacity indicates high efficiency.
- Shorter polishing duration compared to vibratory machines and hand polishing saves time and operational costs.
Low Maintenance and Durability :
- Built with quality materials and designed for durability, reducing maintenance needs and ensuring longevity.
- The use of ceramic mixed media in the polishing process indicates durability and a longer lifespan.
Clean and Safe Operation :
- Produces aluminum power-free, making it cleaner and safer compared to traditional polishing methods.
- Zero safe hazards, ensuring a completely green and eco-friendly working environment.
Superior Finishing Quality :
- Provides a brighter finish compared to traditional polishing machines, enhancing the aesthetic appeal of polished rims.
Ceramic polishing Machine Key Features of Operation:
- Easy to load and unload rims with a pneumatic control system.
- Standard PLC screen control panel
- Center hub and arm rotary speed adjustable.